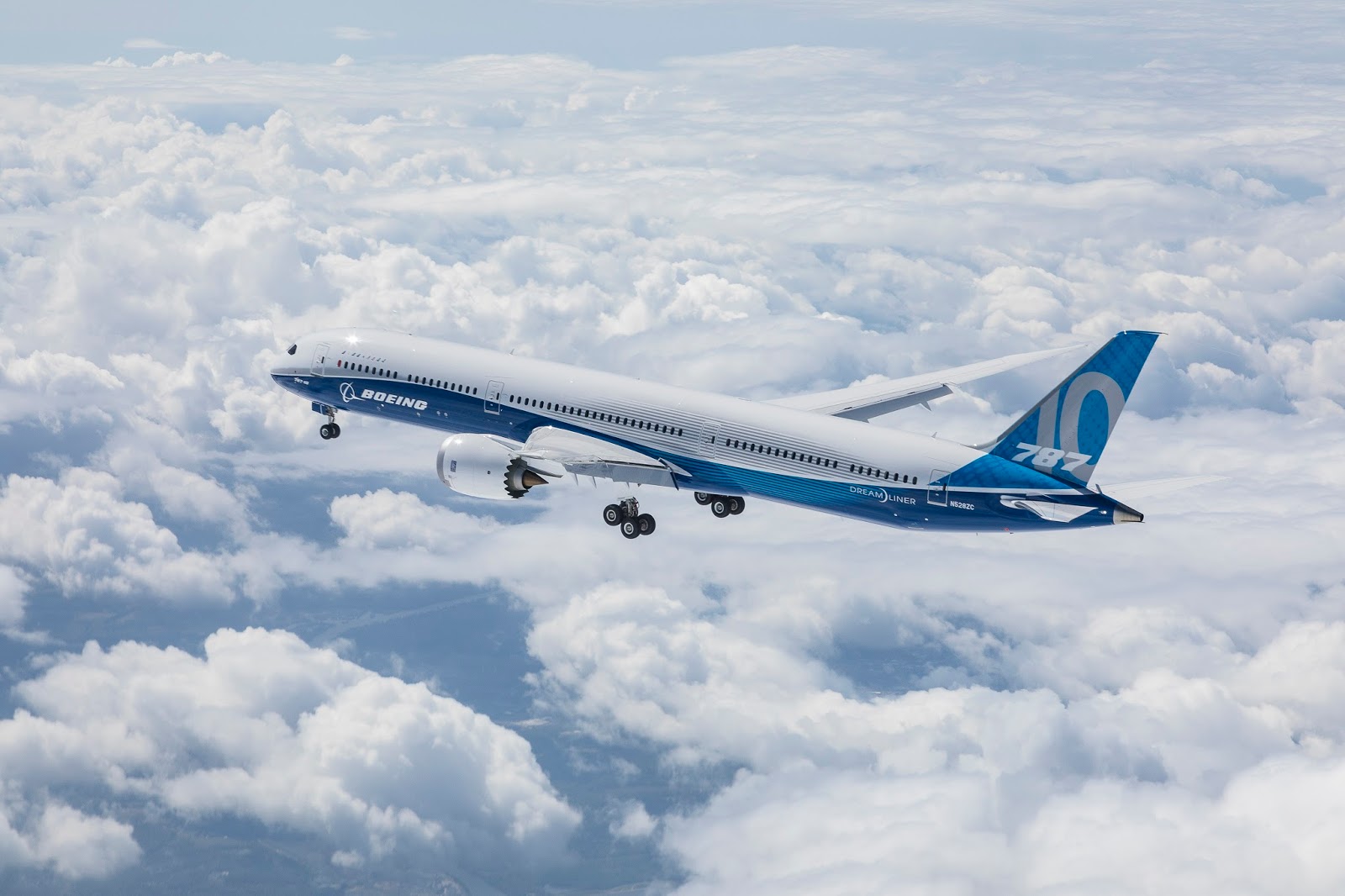
En los últimos tiempos las noticias aeronáuticas no son muy halagüeñas, la covid-19 nos tiene a todos en el suelo, las aerolíneas al borde de la quiebra, los fabricantes sin nadie que les compre los aviones… y el Boeing saliendo contínuamente en la prensa por problemas variados. Los últimos han sido de su avión de plástico, el B-787.
En concreto han salido tres problemas. Uno es de sellado aerodinámico en los timones, al que personalmente y con la información que he encontrado publicada sobre ello, no veo mayor problema que solucionarlo cuando toque cambiar los sellos. Otro es de acabado superficial del revestimiento en la parte trasera del fuselaje, en la zona del mamparo de presión. Una vez más, y con lo poco que he encontrado publicado, no veo mucho más allá de un pequeño problema aerodinámico por no cumplir los acabados superficiales (rugosidad).
Pero hay un tercero que se ha mencionado como shimming, y de este han dicho que puede causar problemas de concentraciones de esfuerzos. Pero, ¿qué es eso del shimming y por qué puede causar problemas?
El shimming no es ni más ni menos que el término en inglés para «suplementado», así como shim no es más que suplemento.
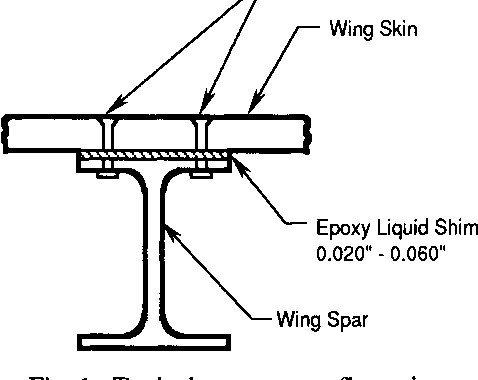
Cualquiera que haya montado una estructura, una estantería, una maqueta… habrá podido comprobar, o sufrir, en sus carnes que la fabricación no es una ciencia exacta. Así, al montar la estructura hay veces que nos toca deformar ligeramente dos miembros para que el agujero del tornillo que hay que poner coincida el de una parte con el de la otra.
Nunca hay dos piezas iguales, aunque estadísticamente hay cierta repetibilidad. Nunca se consigue una dimension o ángulo exacto, aunque estadísticamente se consiguen casi de 90º, y hay que introducir conceptos como tolerancia en longitud, en posición, en planitud… Y esto es especialmente crítico con las piezas de fibra de carbono, donde las tolerancias en espesor son bastante más grandes que con las piezas mecanizadas. Así, mientras que en una pieza metálica mecanizada se pueden lograr tolerancias de espesor realmente finas, con la fibra de carbono nos movemos entorno a un 7% del espesor. Esto es, si en una pieza metálica de 3mm de espesor se pide una tolerancia fina, podríamos lograr piezas que tuvieran 3±0.05mm de espesor. Mientras que en fibra de carbono sería 3±7%=3±0.2mm, tolerancia que en una pieza mecanizada y para ese espesor se consideraría como una tolerancia grosera.
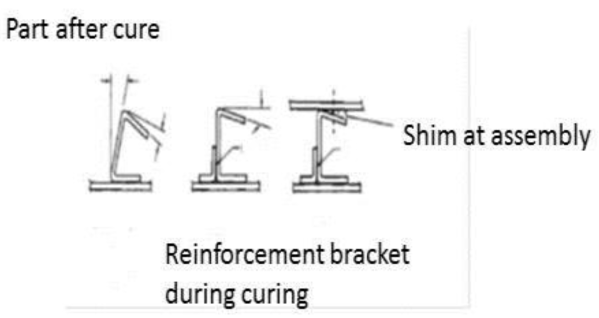
Esta falta de precisión en el espesor hace que los montadores que ensamblan las piezas sufran los mismos problemas que nosotros cuando montamos un mueble, maqueta o estructura en casa. Y los agujeros no cuadran, o la pieza no queda exactamente en su sitio, o… Y la solución inmediata sería forzar la pieza para llevarla a su sitio, como hacemos en casa, ¿no?. Sin embargo el hacer esto haría que la pieza estuviera ya pretensada, con una carga adicional que no se ha tenido en cuenta en el diseño y cálculo de la pieza, porque es una carga que no es normal, o incluso podría deformar la pieza y hacer que no cumpliera su función adecuadamente. Se me ocurre poner como ejemplo una pieza articulada, que al deformarla dejara de girar sobre su charnela sin rozamiento.
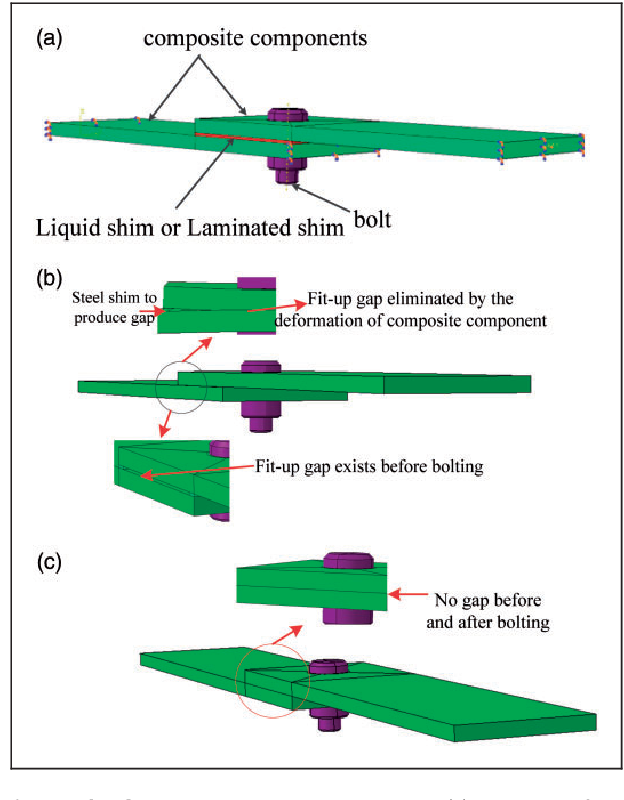
Para solucionar estos pequeños gaps, espacios indeseados, intersticios, que no deberían estar ahí pero que están se utilizan distintas estrategias.
- Si el espacio es inferior a 0.2mm, se utiliza un suplemetno líquido, que rellena el hueco y después solidifica.
- Si el espacio es hasta 1.2mm, se utiliza un suplemento sólido (aluminio, fibra…) en combinación con el suplemento líquido.
- En caso de que el espacio fuera mayor de 1.2mm podría tratarse de un problema más serio de fabricación, y habría que realizar un suplemento de los llamados trabajantes, esto es, un relleno que lleve cargas como una parte estructural más.
- Hay otra estrategia más, que consiste en preveer la necesidad de suplemento durante el diseño de la propia pieza y poner más telas de las necesarias en la zona donde va a ser necesario el suplemento, de tal modo que además de las telas estructurales necesarias para soportar los esfuerzos haya telas «de sacrificio», que puedan ser eliminadas, o peladas, produciendo un suplemento «pelable», y que se ajuste durante el montaje en cada ensamblaje, siendo ésta posiblemente la mejor solución de todas.
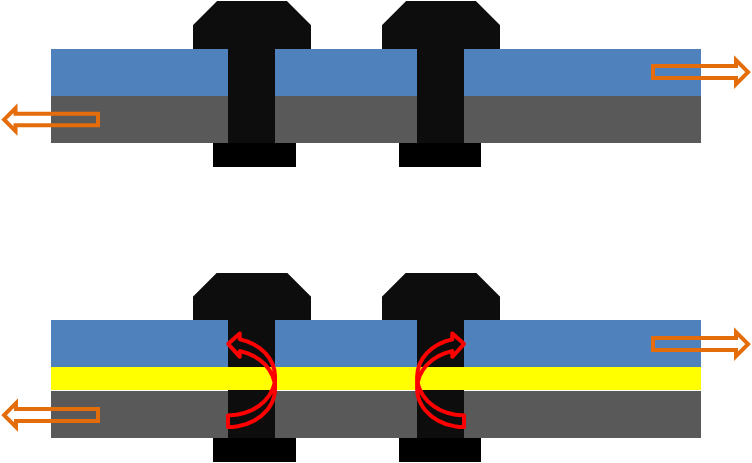
Pero, ¿qué ocurre si este intersticio, palabra que prefiero mil veces antes a gap, es demasiado grande y el suplemento no es trabajante, esto es no lleva cargas, o el suplemento no está instalado adecuadamente?
Sobre estas líneas podemos ver los dos casos. El ideal, y un caso en el que el intersticio es demasiado grande. Idealmente ambas placas estarían en contacto y las fuerzas actuando sobre ellas a cortadura serían transmitidas por los remaches, siendo la excentricidad de la carga despreciable. Sin embargo, cuando el intersticio es grande, sobre los remaches aparece un momento de flexión que sobrecarga el remache así como la placa.
Espero que después de esto haya quedado un poquito más claro por qué al comienzo del todo decíamos que de los tres problemas del 787 que se han publicado, el del sello aerodinámico en el empenaje, el de rugosidad superficial en el revestimiento, y el de shimming, el más problemático pudiera ser éste último.
Fuentes:
- Gracias a este artículo de Wicho en Microsiervos fue donde encontré la noticia original acerca de la rugosidad superficial y de los problemas con los suplementos
- Las fotos, salvo la última que es un esquema propio, vienen de estos enlaces:
- un artículo académico sobre el efecto de los suplementos sobre las estructuras de material compuesto,
- otro artículo académico sobre el uso de microondas para medir los suplementos,
- y una presentación sobre suplementos.
Descubre más desde Sandglass Patrol
Suscríbete y recibe las últimas entradas en tu correo electrónico.