Hace un par de semanas recibimos un correo electrónico de Alejandra Cortés, invitándonos a visitar La Muñoza, los talleres de mantenimiento de Iberia. Y por supuesto, ¡¡no íbamos a decir que no!! Supuse que no íbamos a ser los únicos, así que puse un correo electrónico a Wicho, de Microsiervos y a RPla, de Aire,org y Lo Marraco. Rápido, y entre correos y Twitter localizamos a algunos de los demás asistentes: LandingShort, Surcando los Cielos, Juan de la Cuerva. A los demás nos los encontraríamos allí.
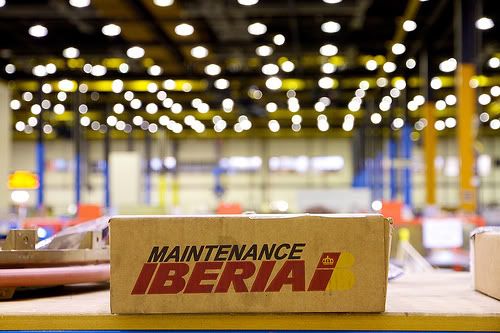
Foto cedida por Nacho Palou, de Microsiervos
Viernes 18, preparamos el equipo… esto es, la cámara compacta. Pensé en coger la reflex, pero luego recordé mi breve paso por mantenimiento, y preferí llevar algo pequeño y que no molestara en taller…
Iberia se encargará de recoger a los bloggers procedentes de fuera de Madrid en el aeropuerto. Los madrileños tenemos la opción de ir a Avenida de América y coger el microbús que proporciona Iberia, o bien ir en coche hasta La Muñoza. Los que tenemos que ir a trabajar después de la visita, escojemos esta segunda opción.
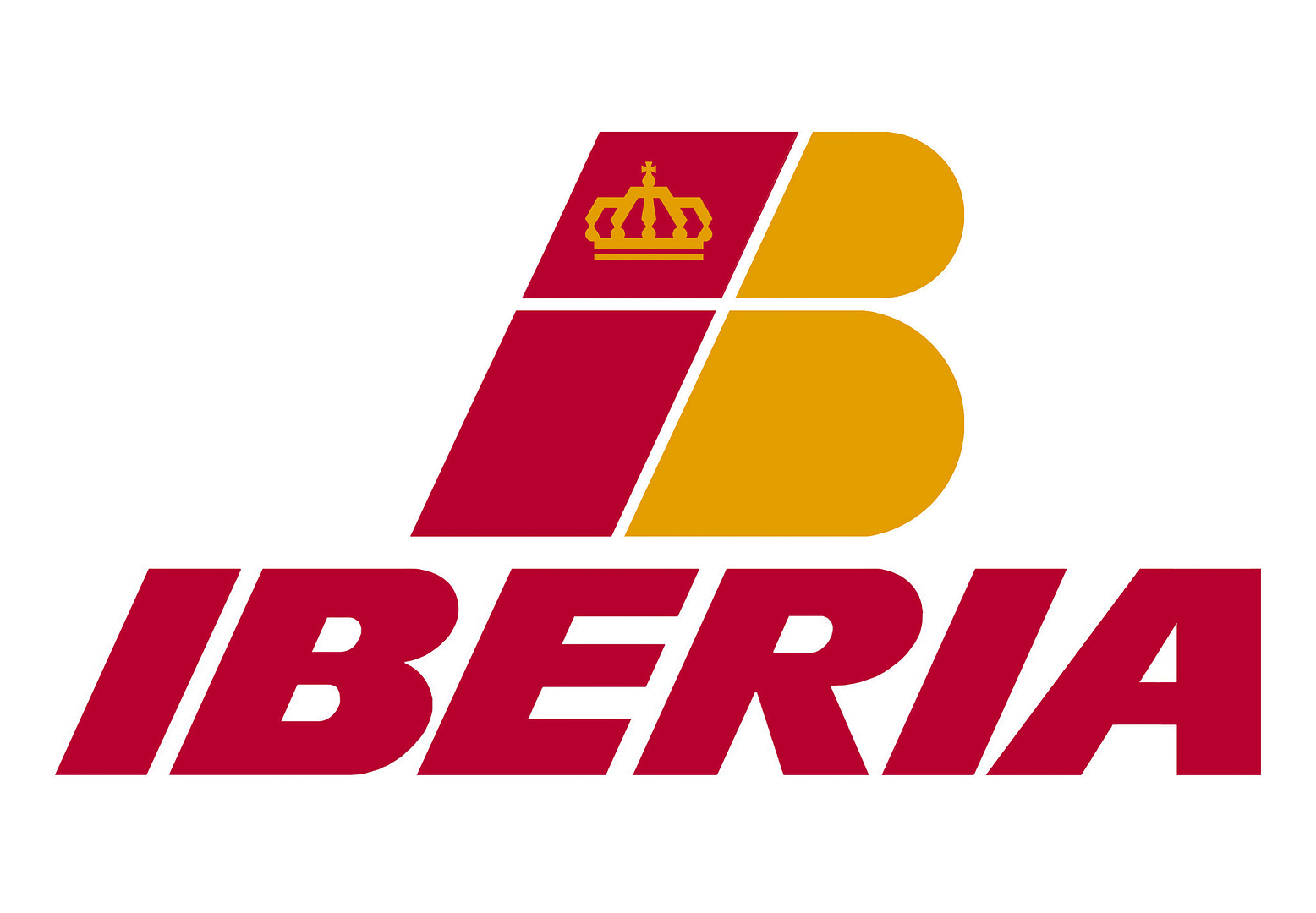
Llego a la puerta de La Muñoza demasiado temprano. Aparco y van apareciendo el resto de los compañeros. Viene a recogernos un coche guía que nos lleva hasta el caserío. Para quien no lo sepa, La Muñoza era una finca ganadera situada a orillas del río Jarama. Iberia compró la finca e instaló allí sus talleres de mantenimiento, que han ido creciendo hasta convertirse en una unidad de negocio más de la compañía, siendo la aerolínea solo el 30% de su facturación, y el 70% restante otras compañías aéreas, así como fabricantes.
Mientras esperamos al resto de los integrantes de la «expedición» visitamos el caserío, ahora dedicado a formación, recepción de visitas, lugar de reunión… Allí hay un pequeño museo de la historia de Iberia, desde fotografías de aviones históricos de la compañía, un diccionario pictográfico que se daba a los pasajeros, o los bolsos de viaje que se regalaban.
También encontramos una rueda y un freno de avión, cortados para mostrar en detalle sus componentes.
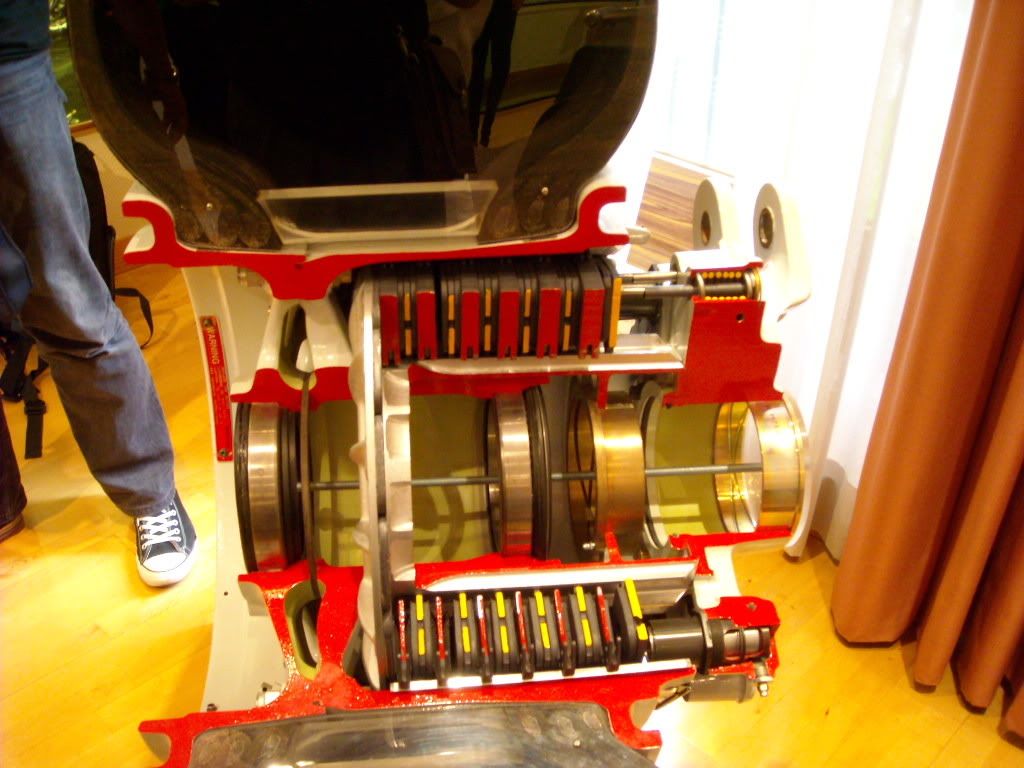
Pertenece a un 747. Pinchad en la imagen para ampliarla. Me hizo recordar los tiempos en los que me llegaban los frenos de los DC8-62 y -73 y había que hacerles el overhaul o el cambio de pastillas. En la imagen podéis observar el neumático; la llanta, compuesta de dos semillantas y una junta de estanqueidad; A la derecha está el freno, con el piston housing, y los discos de stator y de rotor. Los discos de stator están intercalados con los de rotor. En todos hay una serie de pastillas, con forma de sector de corona ciruclar, sujetas con un remache. Cuando el skydrol, el líquido hidráulico, empuja los pistones, éstos empujan los discos que giran contra los que no, haciendo frenar la rueda.
Mientras comentaba estos detalles con algunos de mis compaleros de visita, llegaron los demás. Entonces Iberia nos ofreció un suculento desayuno. Algunos de mis compañeros decidieron salir a la terraza, para ver los aviones. Otros nos quedamos charlando, ¡¡es que hacía mucho que no nos veíamos!!
De allí partimos al taller de mantenimiento de motores, con un libro sobre la historia de La Muñoza, obsequio de Iberia.
Allí dimos una vuelta, viendo los motores aún sin desmontar
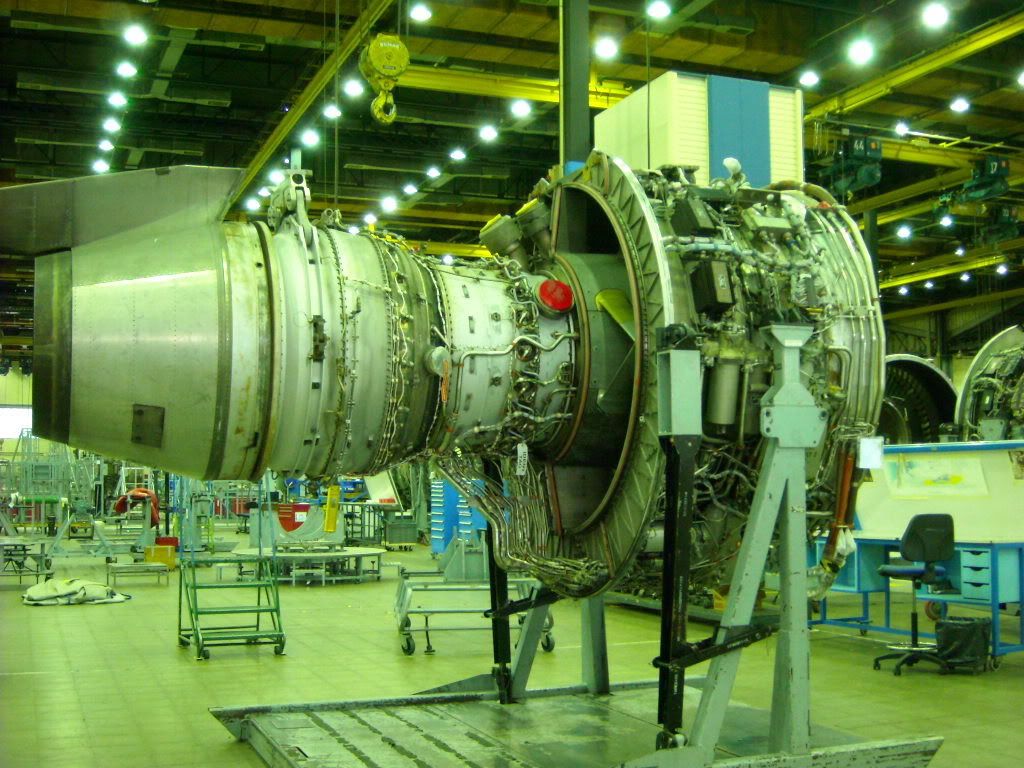
Y paseamos entre ellos, acercándonos para ver todos los detalles que podíamos y nos llamaban la atención: los álabes de titanio, los complejos mecanizados que se observan en algunas piezas… y hacer fotos a otros visitantes que a su vez hacían fotos… (este es Nacho, de Microsiervos).
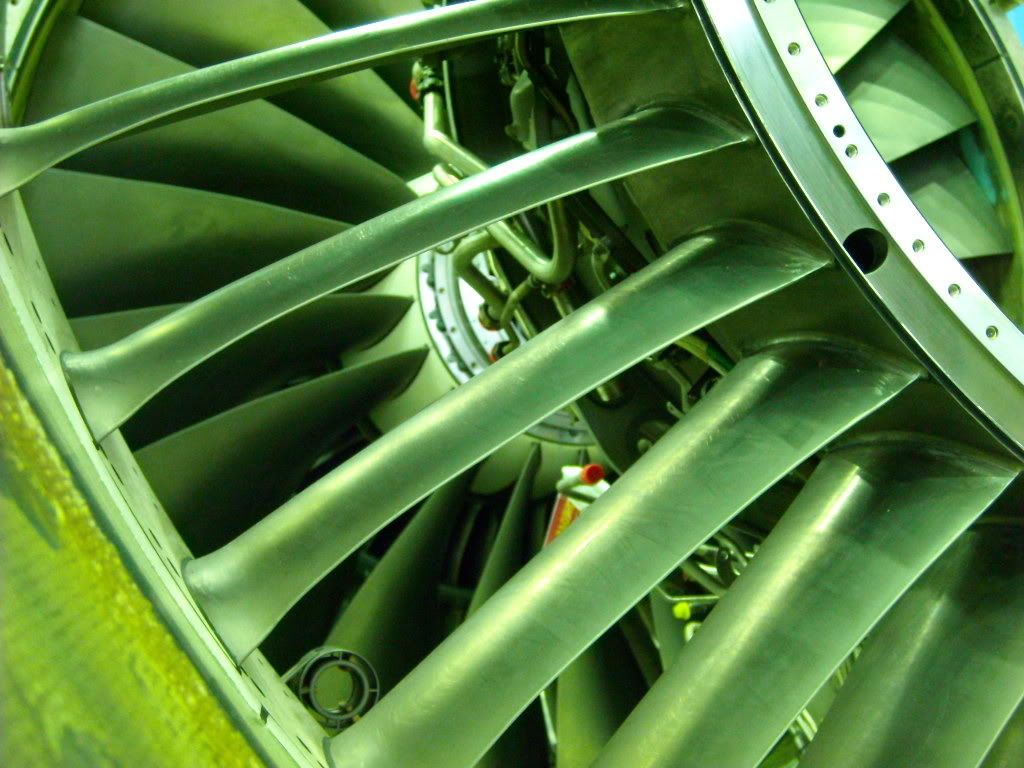
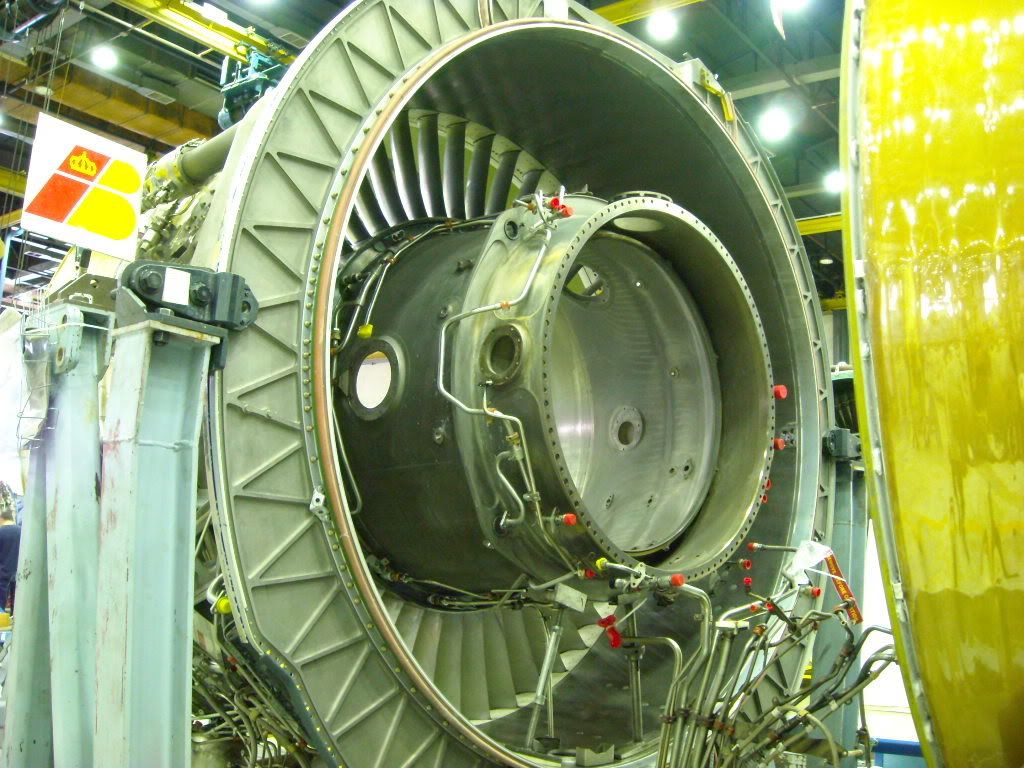
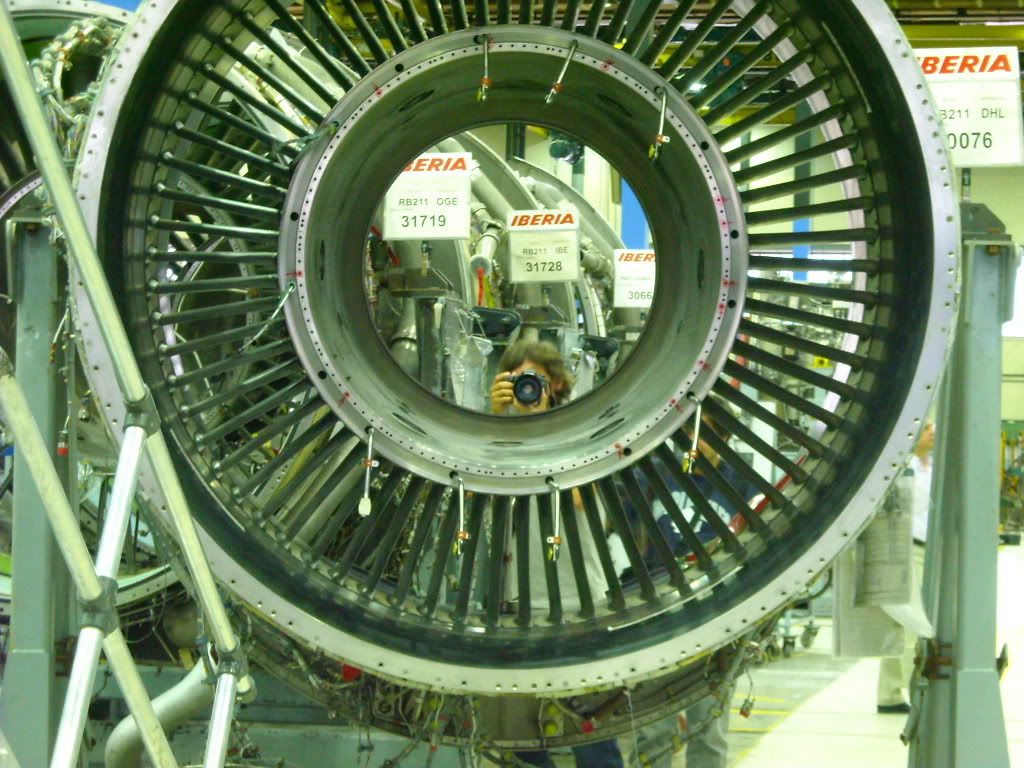
Tras cotillear un poco libremente lo que habíaa nuestro alcance, llegó Esther, una ingeniero aeronáutico a explicarnos a todos los presentes el taller, y acompañarnos en todo el recorrido.
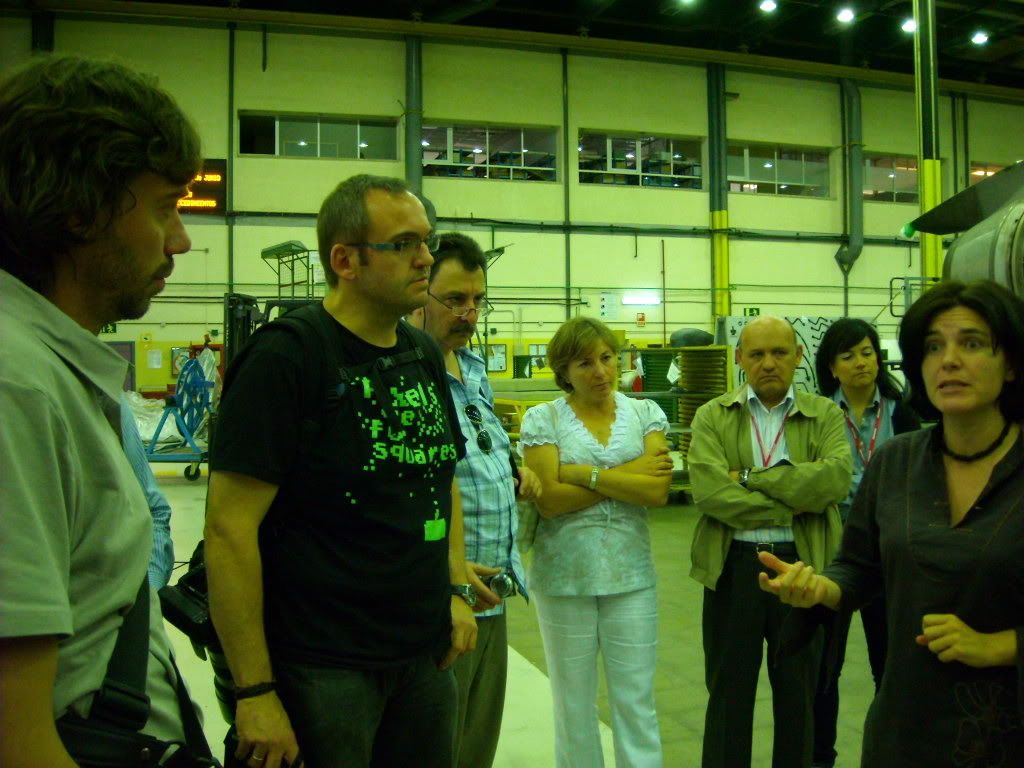
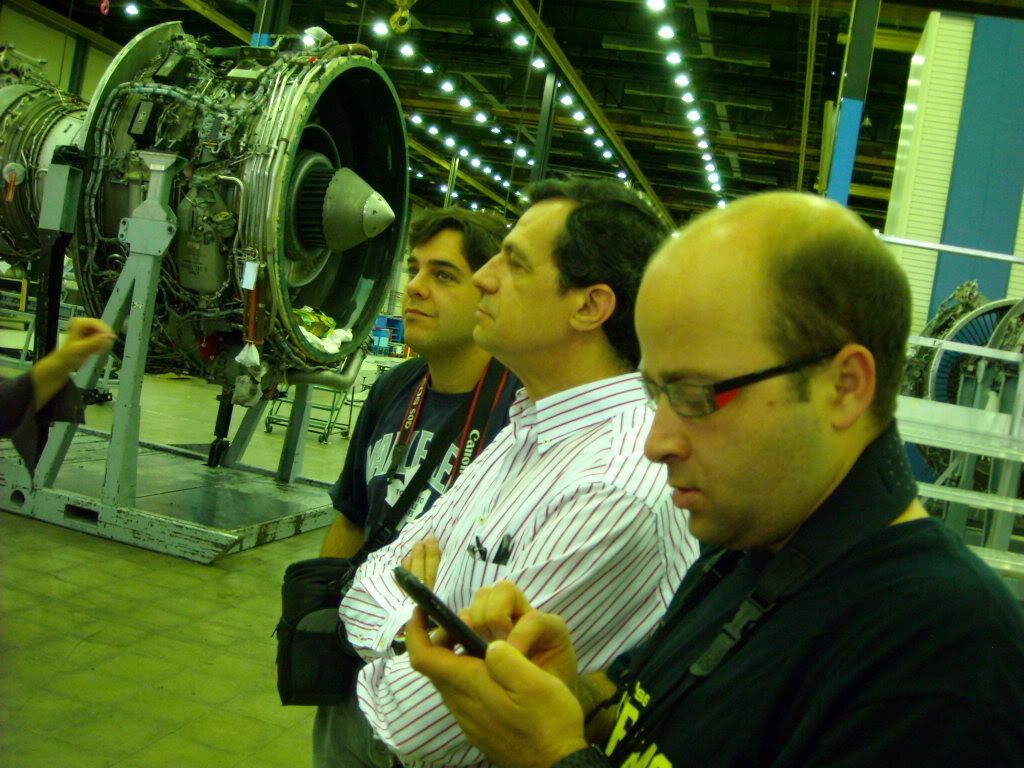
Esther nos contó aquí algunos datos económicos del mantenimiento de motores: el 70% de los clientes de Iberia Mantenimiento son compañías aéreas y fabricantes de motores, solo el 30% del trabajo es procedente de la línea aérea Iberia.
Los motores son desmontados del avión, y transportados a alguno de los pocos aeropuertos de carga existentes en Europa. Desde allí son transportados en camiones hasta La Muñoza, donde son recibidos, desmontados pieza a pieza y limpiados. Tras un proceso de optimización de tiempos, o de cadenas de montaje-desmontaje, o de organización del taller, como se quiera, se ha logrado una capacidad de hasta 250 motores al año. El proceso de revisión completa del motor es de algo más de 2 meses. También nos explicó el funcionamiento de un turbofán con alto índide de derivación, pero como sois fieles lectores nuestros, sé que ya habéis leído el artículo donde os explicamos eso, y no voy a repetirlo aquí. También nos explica que el motor puede ser desmontado por mantenimiento programado o no programado. En caso de mantenimiento programado, y en general en aviación, puede ser por haber cumplido un número determinado de ciclos o de horas de vuelo. O como resultado de otras medidas de desgaste, como testigos de desgaste en los frenos, o la temperatura de determinada sección en el motor.
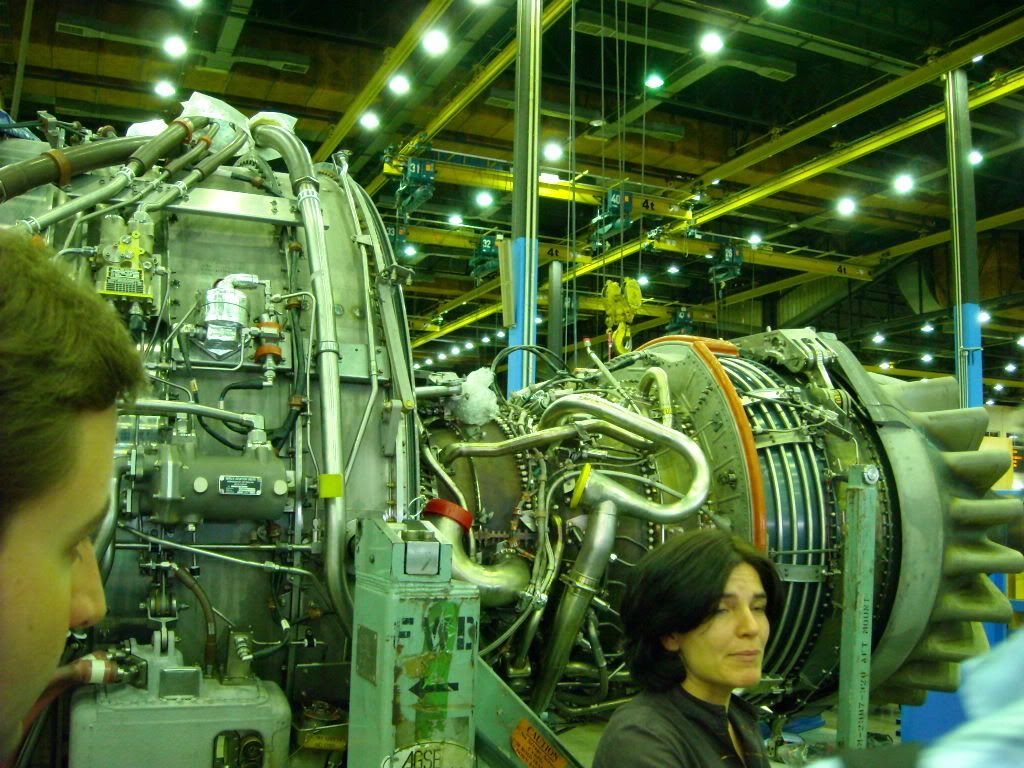
Cuando el motor llega, se desmonta el fan cowl, el capó, que se mantiene en el hangar de estructuras. El resto del motor va al taller de motores, donde se despieza y se cataloga en cajas. Como es propio de los talleres de mantenimiento, cada pieza -cada p/n o part number, es identificado y colocado en un lugar determinado. De ahí pasa al lavavajillas. Sí, tal cual, una especie de lavavajillas industrial y robotizado, que automatiza el proceso de lavado, reduciendo los cuellos de botella que se formaban cuando se hacían a mano.
Del lavavajillas pasamos a la zona de END o NDT, esto es Ensayos No Destructivos o Non Destructive Test. Aquí las piezas son inspeccionadas de diversas formas:
- visualmente: la pieza se inspecciona ‘a ojo’, en busca de desperfectos, golpes, corrosión… Esta inspección es especialmente llamativa cuando se realiza con boróscopo o endoscopio.
- por partículas magnéticas: si el material puede ser imantado, se imanta. Después se le echan por encima limaduras de hierro, o mejor dicho, unas partículas magnéticas con una forma determinada: las esféricas favorecen la movilidad, las cilíndricas favorecen su alineación con los campos eléctricos. Si existiesen grietas, las partículas se distribuirían de una forma concreta entorno a estas, por la distorsión que hacen las grietas del campo magnético.Tras la inspección la pieza a de ser sometida a un ciclo de desmagnetización, pues si la pieza permaneciera imantada podría causar problemas en el avión, por ejemplo con los instrumentos de navegación. Las partículas magnéticas pueden estar coloreadas con tintes que reaccionan a la luz ultravioleta, para una mejor inspección. ¡Ah!y cuando se hace esta prueba…¡¡hay que recordar entrar sin reloj!!
- por líquidos penetrantes: las piezas son literalmente bañadas en un líquido. Si existen grietas el líquido se acumulará en ellas. Tras este baño, la pieza es lavada. En función del tipo de líquido se echará un polvo fino o revelador que absorverá el líquido de la grieta y la hará visible, o bien se iluminará con una luz ultravioleta. Tras la inspección, las piezas serán lavadas para eliminar cualquier resto contaminante de ellas.
- Por Rayos X, aunque de esta creo que no tengo que explicaros nada. En tiempos estuvo bastante en boga la inspección por rayos gamma, puesto que el aparato para generarlos es mucho más pequeño y además es portable. Sin embargo, los rayos X se ‘apagan’ al apagar el equipo. Los rayos gamma se generan con un isotopo radiactivo aislado en una celda segura, y no se ‘apagan’, solo se cierra la célula para impedir que escapen de ella radiaciones.
- Corrientes inducidas: con un palpador se inducen corrientes en la pieza a inspeccionar, y éstas se distorsionan o no en función de los defectos que tenga la pieza inspeccionada.
- y por ultrasonidos, básicamente una ‘ecografía’ de la pieza.Un palpador emite un ultrasonido, que atraviesa la pieza, y que devuelve uno u otros ecos en función de los daños que encuentre dentro (grietas, delaminaciones si hablamos de fibra de carbono…).
Fotografías cortesía de Iberia
¿Cuál es mejor? ¿Por qué tantas inspecciones? Pues todo depende de qué se vaya a inspeccionar. Con líquidos penetrantes solo se detectan defectos superficiales, no internos, y no son válidos para inspeccionar fibras de carbono o vidrio; las partículas magnéticas detectan defectos superficiales y sub-superficiales, pero se requiere que el material sea magnetizable; la inspeccion visual se limita a daños de cierta consideración, las corrientes inducidas requiere que el material tenga ciertas propiedades, con los ultrasonidos no se pueden inspeccionar correctamente los bordes debido al ‘efecto borde’, esto es, lecturas de defectos que no existen y que se deben a la proximidad a un borde.
Una vez detectados los defectos, se pasa a la clasificación de los daños, como vimos en la entrada Daños Admisibles, no Admisibles, Reparaciones Temporales, Permanentes, Cosméticas o Estructurales. Y HST.Esto es, el daño puede ser no reparable (estar más allá de los RDL o Repair Damage Limit), y entonces la pieza será considerada scrap, puede ser un daño admisible, y entonces se sanea el daño (se para la grieta, se elimina la misma…) y se realiza una reparación cosmética, y si está más allá de estos límites (ADL, Allowable Damage Limit) se planteará una reparación estructural. Todos estos límites, así como formas de reparar, están contemplados en el manual de reparaciones del avión.
Pedi ver alguna pieza de scrap o alguna que tuviera un daño o estuviera en reparación, pero esto no fue posible. He trabajado tanto en mantenimiento (frenos, ruedas, baterías, balsas, chalecos, botellas de oxígeno…) como definiendo reparaciones estructurales de fibra de carbono, y por tanto ya he visto esto. Pero no he podido hacer nunca fotografías por razones de confidencialidad. Me parecía una buena ocasión para que otros aerotrastornados pudieran verlo, pero no fue posible.
Lo que si pudimos ver fue algunas piezas, que aprovechamos a fotografiar en detalle. Aquí se puede ver un álabe. Y debajo podemos observar como hay álabes huecos, para permitir la refrigeración de los mismos.
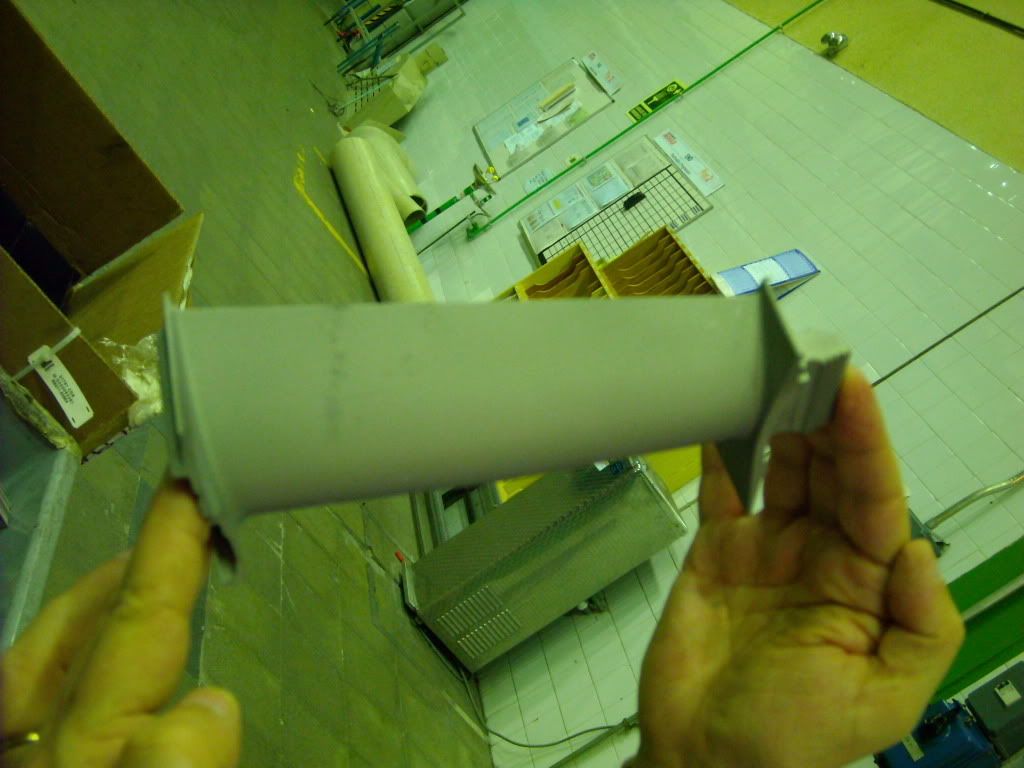
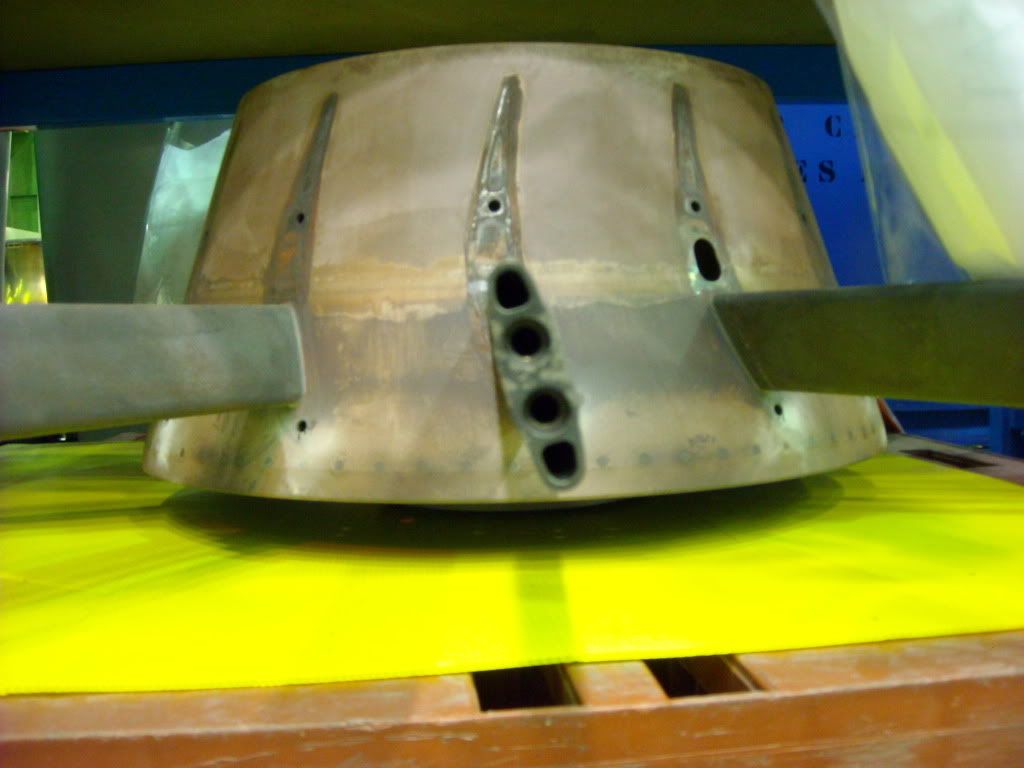
De aquí pasamos a la sala de verificación dimensional. Aquí, una vez más, volvi a mi época de universidad y de trabajar en mantenimiento. Recordar conceptos de calibración y cómo se usaban esas máquinas. La sala ha de ser una sala de temperatura controlada. Las piezas a verificar son metálicas, así como muchas de las piezas de las máquinas que han de verificar sus dimensiones. Por ello, debido a que los metales son muy sensibles a las variaciones de temperatura y se dilatan o contraen con el calor y el frío, se utiliza una sala de temperatura controlada. Todas las mediciones realizadas son dependientes de esta variable, temperatura. Las piezas son medidas en varios de sus diámetros, y así se comprueba cómo de perfecta es su circunferencia (cómo de redonda es) y si está dentro de tolerancia o no.
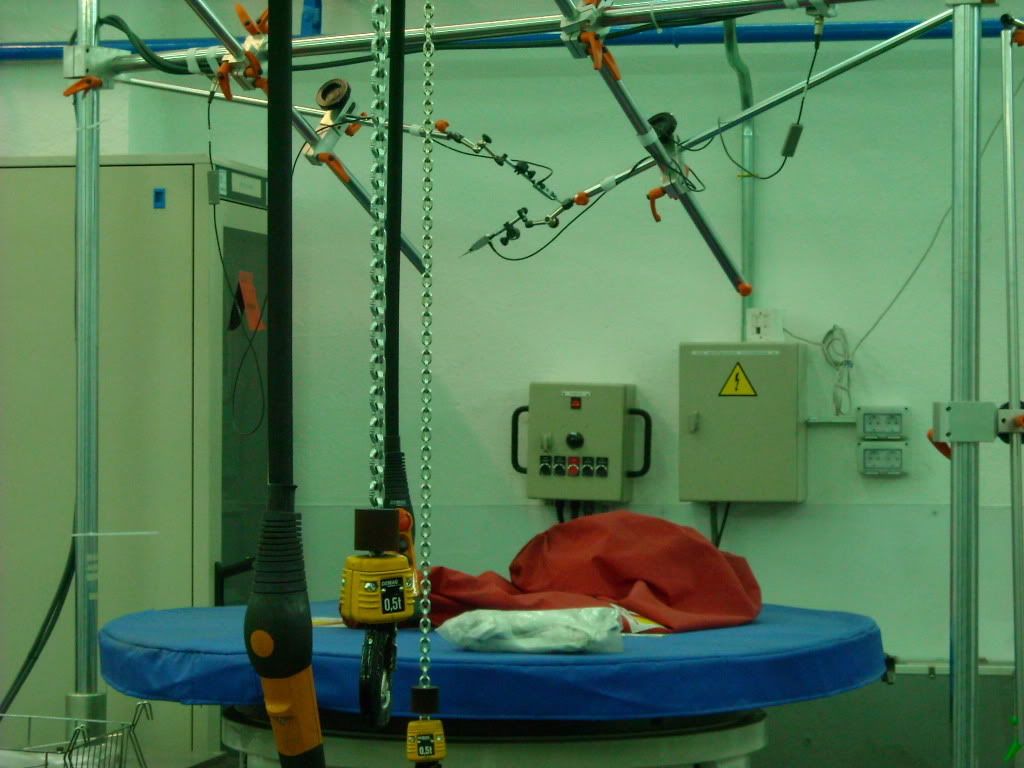
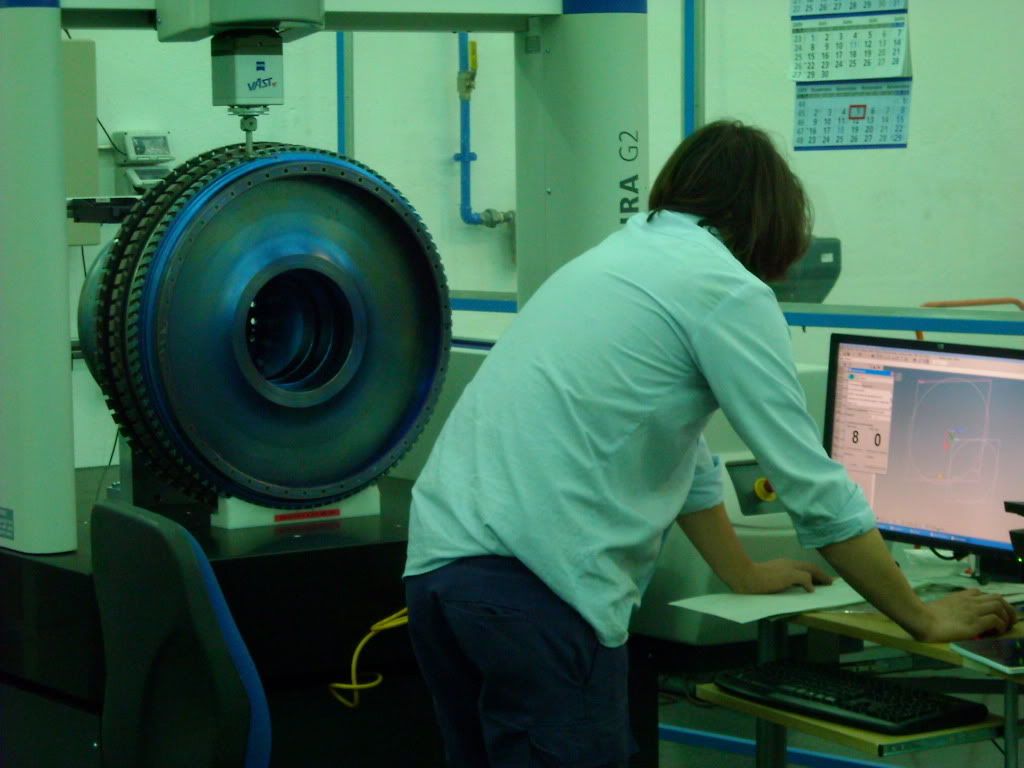
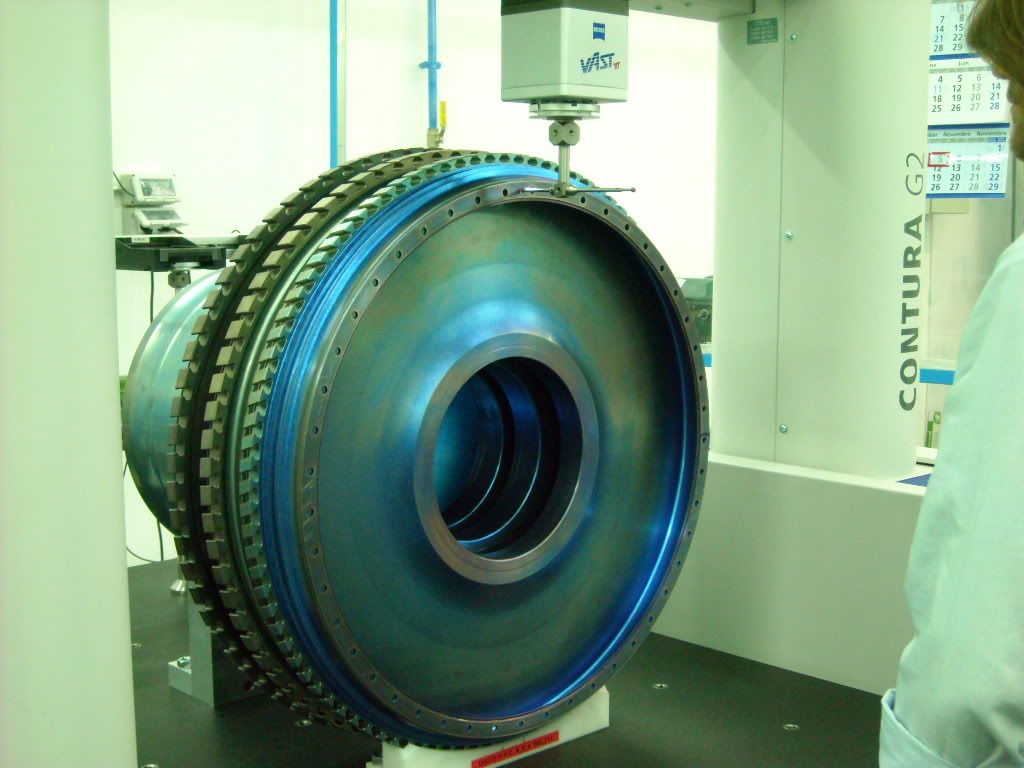
De allí pasamos a ver una tecnología que llamó especialmente mi atención, y que no pude fotografiar. Así que en cuanto uno de mis compañeros publique la foto, se la robaré para ponerla en el blog. Se trata de la reconstrucción de álabes o discos por medio de recrecido con material de aporte proyectado en estado de plasma. El recrecido puede realizarse mediante soldadura, pero en este caso el material de aporte y el material a recrecer quedan «separados», la unión es frágil. Sin embargo, si el metal de aporte se calienta hasta convertirlo en plasma y se lanza en estado iónico contra el metal a recrecer, se forma material unido como si ambas partes se hubieran generado juntas, del mismo tocho metálico o en la misma colada de fundición.
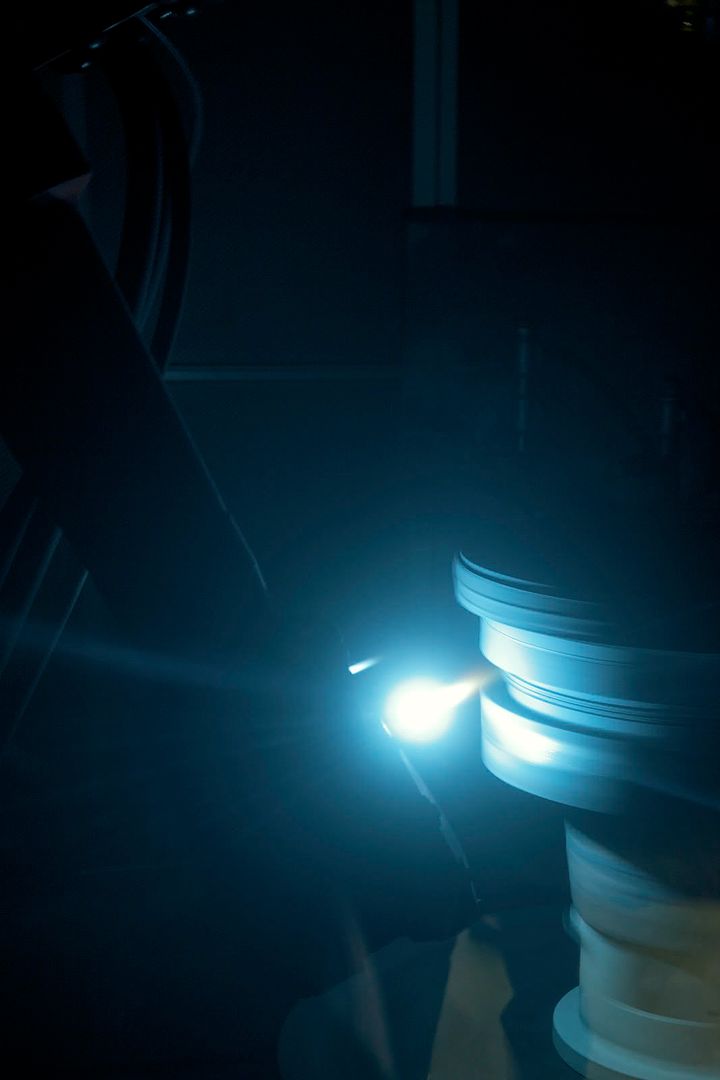
Foto del recrecido por plasma, cedida por Alvarito, para este resumen.
Tras el recrecido, el acabado superficial del metal es muy rugoso. Y así como la tolerancia dimensional es muy ajustada y ha de ser verificada, el acabado superficial ha de ser muy fino, y es necesario mecanizar las piezas para obtener la rugosidad superficial adecuada. Esto se hace mediante una máquina de mecanizado conocida como rectificadora, como la que podéis ver en la imagen.
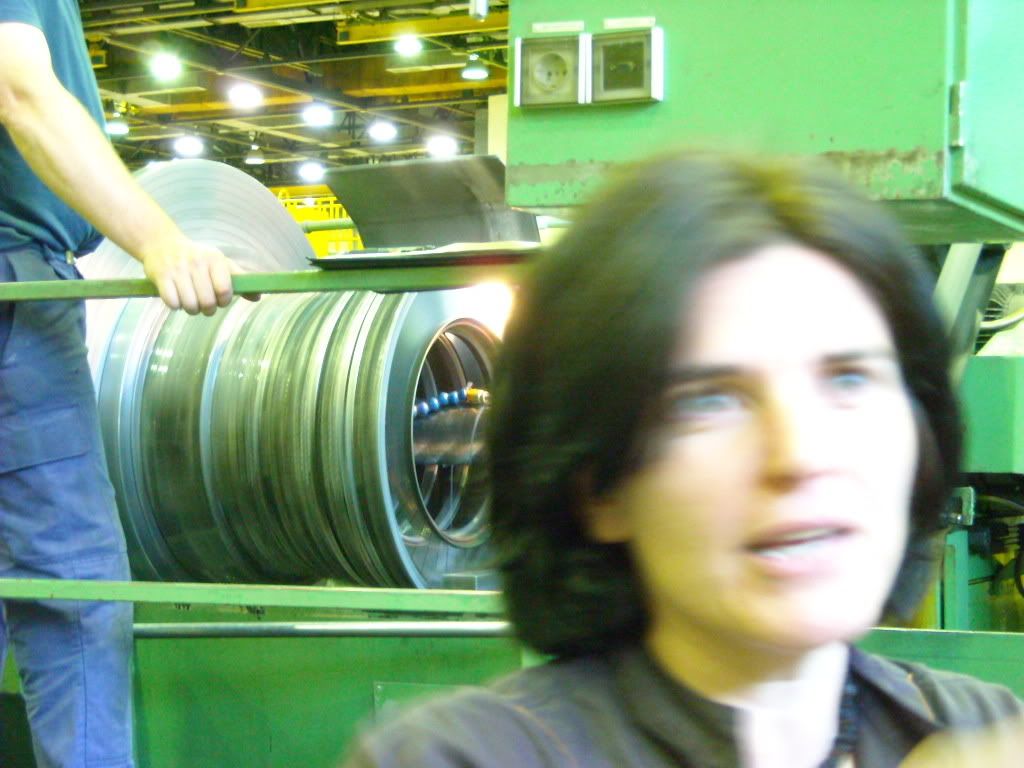
(sí, la foto no es de calidad, en cuanto tenga disponible otra mejor, la pongo).
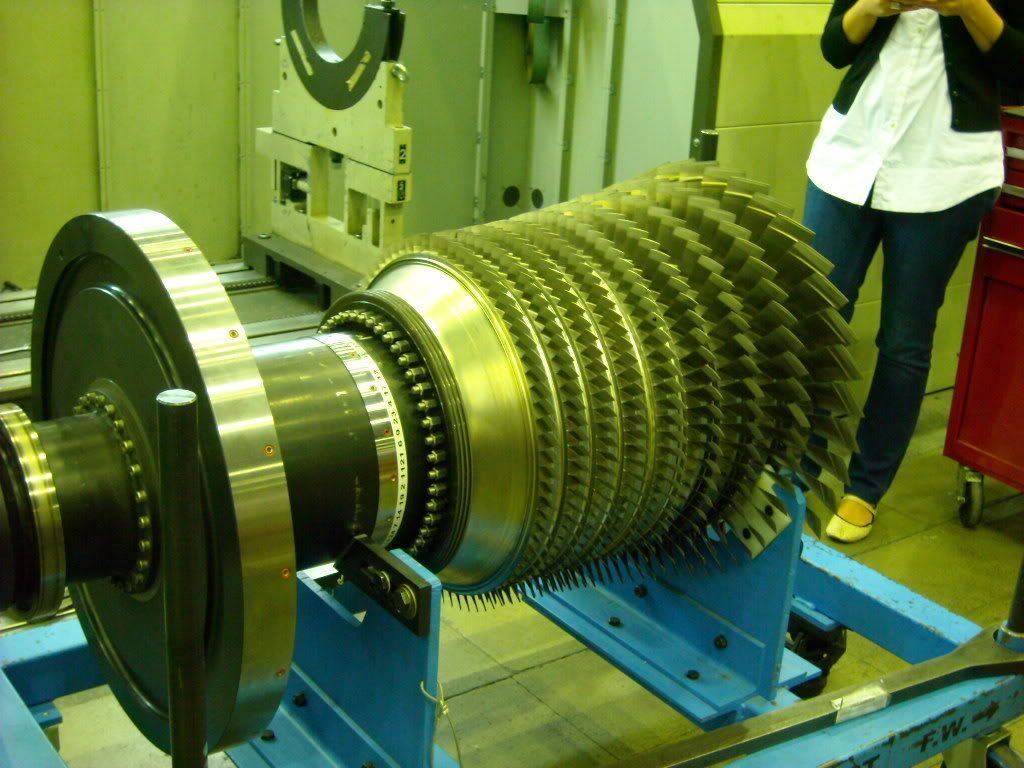
Una vez concluidas estas labores, se procede a volver a montar todos los componentes. Igual que las ruedas de los coches, que van equilibradas dinámicamente con plomos para evitar vibraciones, todas estas piezas giratorias han de ser equilibradas. Además las revoluciones a las que giran no solo podrían provocar vibraciones, ¡si no su completa destrucción! Y es que estamos hablando de piezas que giran en un orden de magnitud de hasta diez mil revoluciones por minuto.
¿Y creéis que con esto hemos terminado? Aun falta probar el motor en el banco de pruebas. El bancode pruebas es un edificio enorme y vacío, con una entrada de aire en un lateral, y con otra salida de aire situada detrás del motor, y generalmente orientada hacia el techo, de tal forma que se obliga al chorro de aire a hacer un codo, perdiendo energía y silenciando un poco su salida. Cuando el motor se introduce en el banco, se hace carenado, simulando las condiciones de vuelo reales del motor.
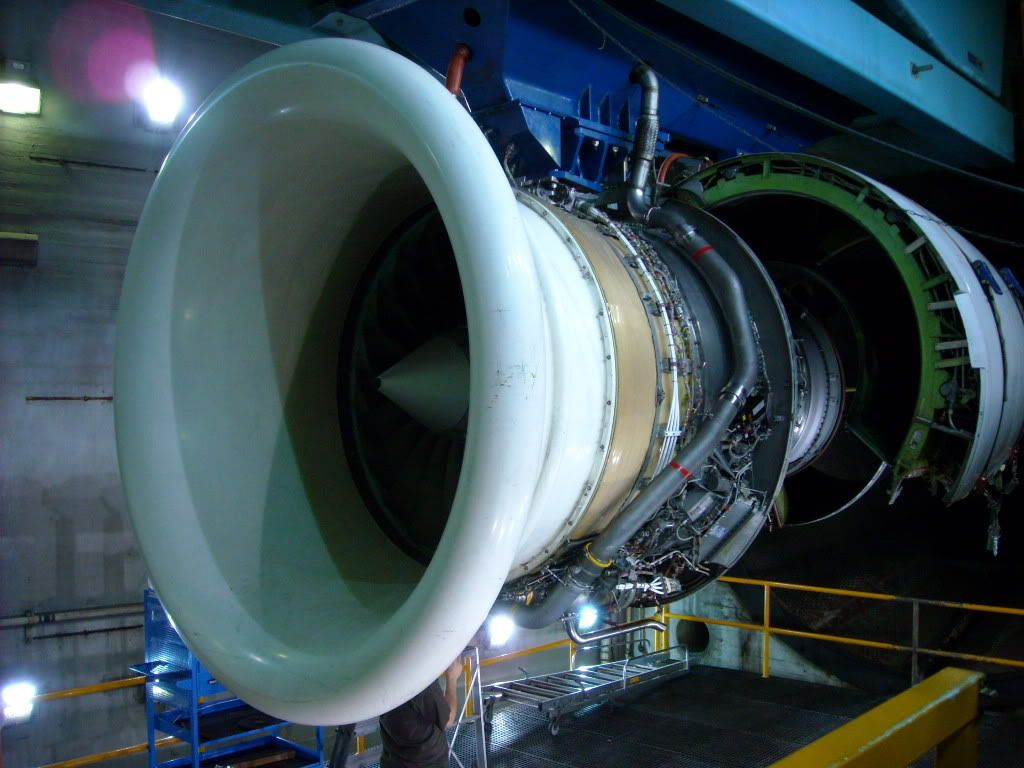
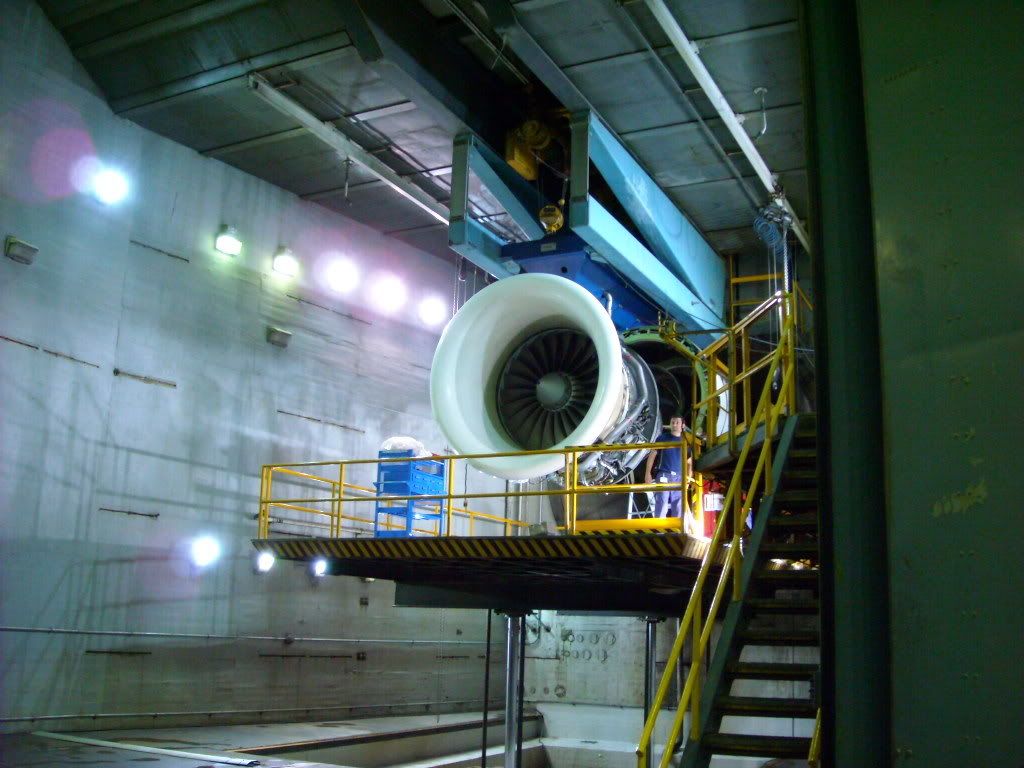
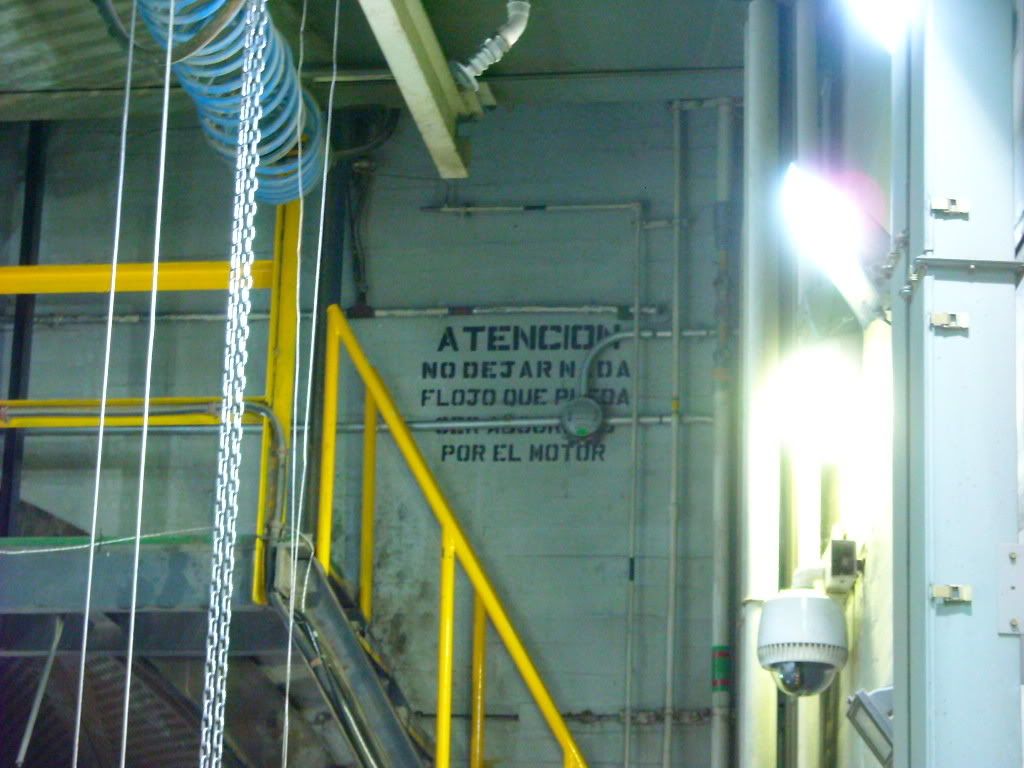
Desde la sala de control se monitorizan todos los parámetros que son necesarios para garantizar que el motor sale en condiciones de aeronavegabilidad del banco de pruebas: revoluciones de las distintas etapas de compresor y turbina (N1, N2, N3…), temperaturas, empuje, vibraciones. Además de ser correctos, estos valores han de estar a cierta distancia de un valor umbral, que es el que marcaría que el motor ha de ser desmontado para revisión.
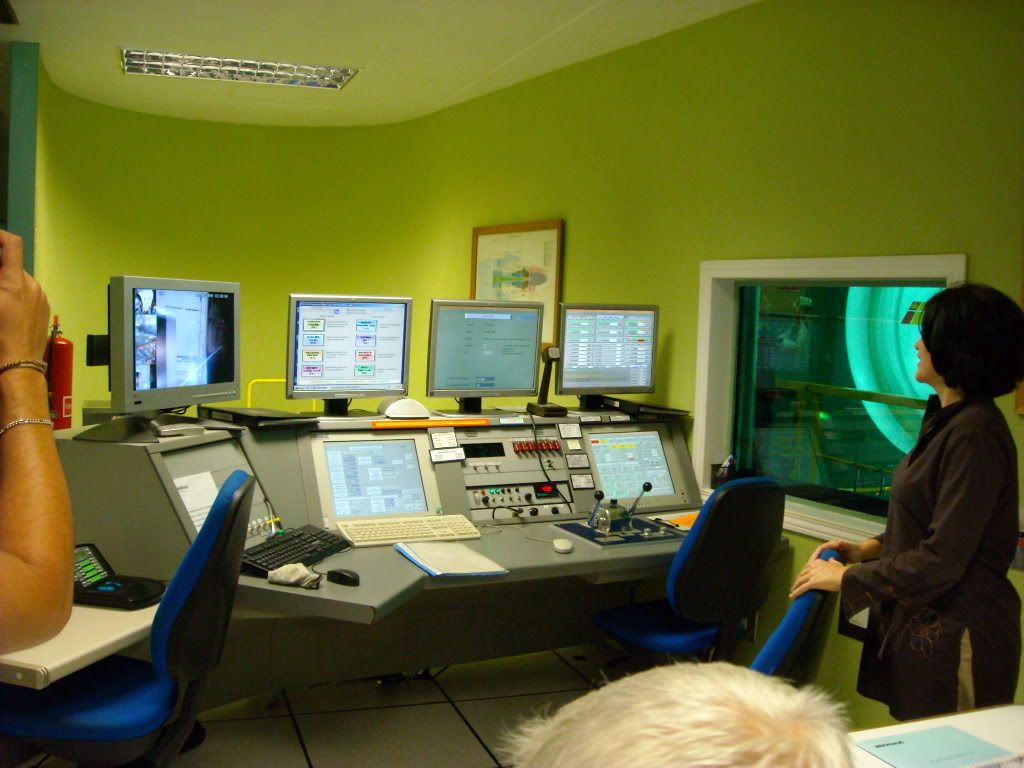
Como toda herramienta de medición que se precie, el banco ha de ser calibrado. Un motor medido en un banco en Madrid, otro en cualquier otra parte del mundo, no tiene por que dar los mismos resultados. Incluso si el mismo banco estuviera en dos localizaciones distintas, con el mismo motor, daría distintas mediciones. Es por ello que existen los llamados Bancos Madre, donde los fabricantes realizan las mediciones en sus motores. Estas mediciones son tomadas por válidas, y los Bancos Hijo son calibrados para que den las mismas mediciones que los bancos madre. Los centros de mantenimiento comparan las mediciones de sus bancos respecto a estos Bancos Hijo, y realizan los ajustes de calibración correspondientes para que las medidas realizadas sean buenas.
Completada la visita al hangar de motores, nos despedimos de Esther y nos dirigimos al hangar 6, donde nos recibe Alfredo. Al entrar en el hangar compruebo que me he quedado sin batería en la cámara de fotos, y que Jota ya se ha ido porque tenía que ir a trabajar. Esto me pasa por fiarme de ‘no, si la batería la tengo cargada…’. ¡Y por no pedirle su cámara! Por eso, el final de mi relato carecerá de fotografías, al menos hasta que se las pueda quitar a algún aerotrastornado (con su permiso, claro).
En el hangar encontramos varios aviones, 320 y 340, en diversos estadíos de su mantenimiento. Vale, lo reconozco, soy incapaz de diferenciar a simple vista si se trata de un 318, un 319, un 320 o un 321, así que me referiré aquí a ellos como ‘320‘, que es el nombre de la familia. Es grato ver de cerca las puertas del tren de aterrizaje que tantas veces he visto en proceso de fabricación en Aries Complex, empresa en la que he trabajado hasta hace poco. También es curioso ver un 340 desprovisto de todos los paneles de material compuesto de su belly fairing, dejando a la vista los larguerillos y cuadernas que forman la estructura de la belly, así como los sistemas que esta aloja. Hay alguna que otra mancha de skydrol en el suelo, y su olor me recuerda ciertas operaciones de verificación de los frenos que realizaba en Palma de Mallorca.
Subimos a un 320 de iberia, totalmente vacío, y comprobamos qué aspecto tiene el suelo, de material compuesto y estructura sandwich, sin vestir, o el aislamiento de las paredes y distintos conductos de aire acondicionado. Nos cuenta Alfredo que se tarda apenas un día en desnudar todo el avión por dentro.
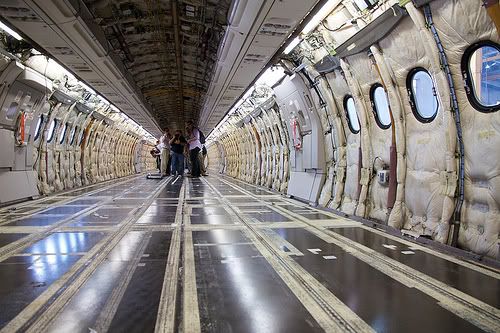
Foto de Nacho Palou, de Microsiervos
Al final la profesión tira, y le hago unas preguntas técnicas a Alfredo. Le pregunto si las reparaciones en fibra de carbono se realizan en la propia Iberia o si se realizan fuera. Nos explica que Iberia tiene su propia DOA (Design Aproval Office, en Interiores y modificaciones de cabina -remodelaciones y modificaciones clase business, turista, …-), y que por tanto puede proponer las reparaciones al fabricante. También pregunto si las reparaciones en fibra de carbono se realizan remachadas o capa a capa, y me confirma que se realizan capa a capa. Y no, no tienen autoclave. Para los que no hayan entendido una palabra de lo que he dicho, la fibra de carbono es una tela o una cinta hecha de este material, apilada con distintos ángulos, y embebida en una matriz plástica (termoestable, como norma general) que le da su forma. Cuando se daña, se delamina (se separan unas capas de otras) hay que reparar. Y existirían dos formas de hacerlo: sanear el daño recortándolo y parcheando sobre él con un parche remachado, o bien eliminando las capas una a una hasta eliminar el daño, y posteriormente reponer todas las capas y curarlas, sometiéndolas a un ciclo de presión y temperatura.
Me llama la atención en este hangar un avión sobre gatos. El avión, para mantenimiento, tiene que ser izado en ocasiones. Y no puede realizarse este izado desde cualquier punto del avión. Todo avión tiene unos puntos diseñados y calculados en su estructura para izarlo. Este avión estaba elevado con gatos desde los puntos situados en las alas y en el morro. Su alzado posterior, esto es, mirándolo desde atras, nos dejaba una curiosa imagne, con las alas flexionadas hacia arriba.
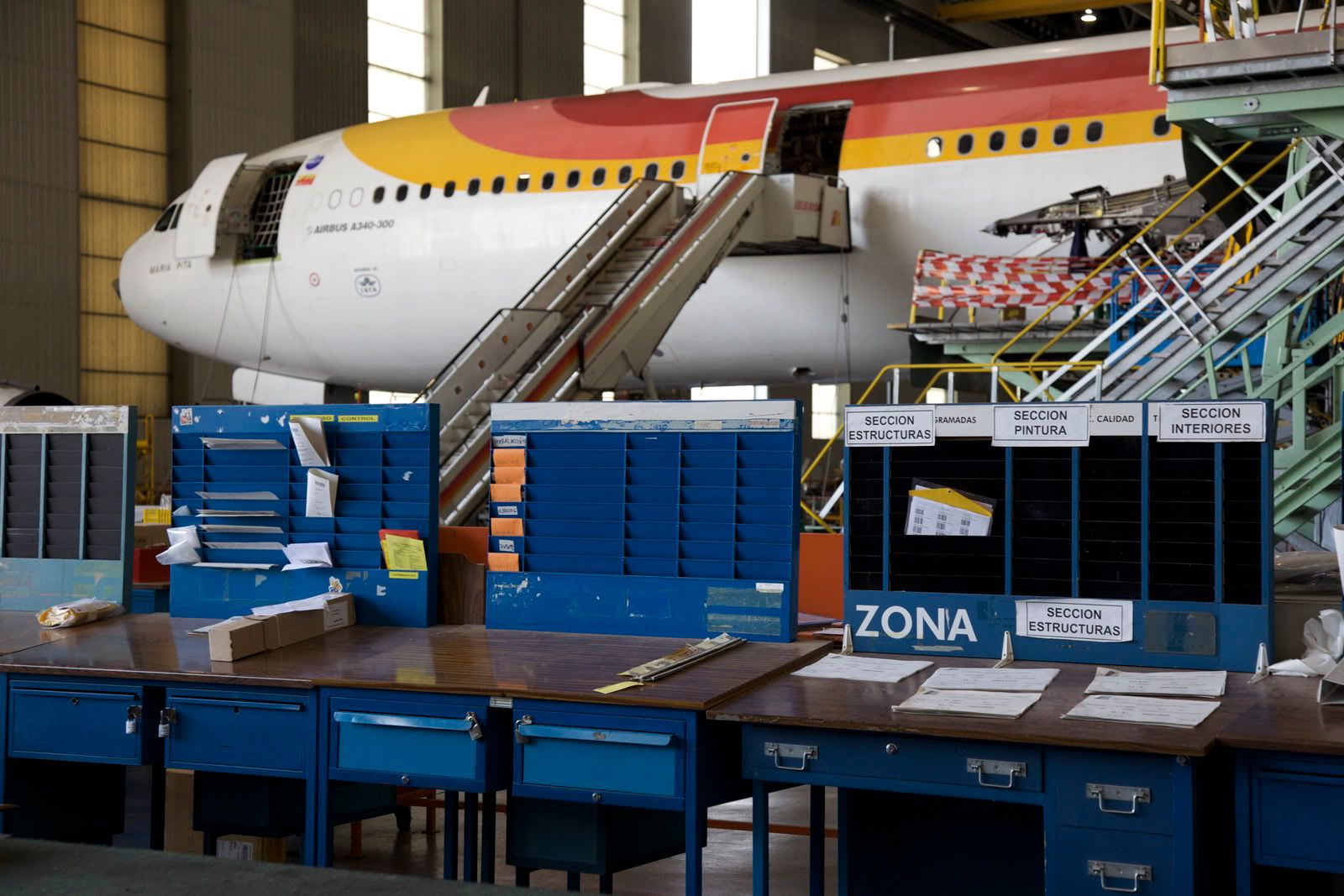
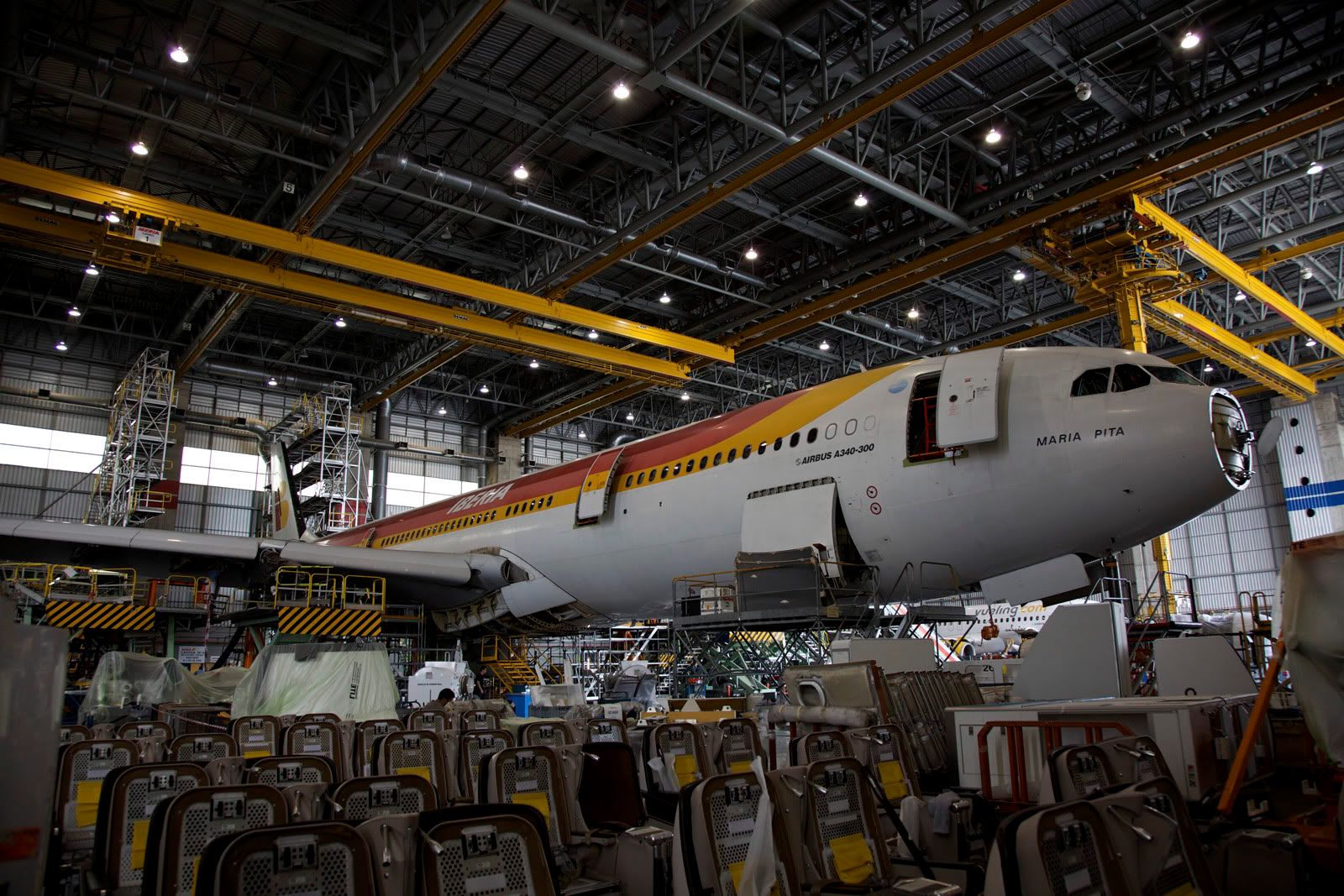
Foto del recrecido por plasma, cedida por Alvarito, para este resumen.
Y hasta aquí dio la visita a la Muñoza. Nos despedimos de nuestros anfitriones, que nos regalaron una maqueta escala 1:200 de un A320 y una carpeta con datos económicos de la compañía. Habíamos consumido todo el tiempo disponible, y tuvimos que salir del hangar y dirigirnos, unos a comer, otros a trabajar.
En cuanto consiga las fotografías de Jota las publico. Y en cuanto tenga permiso de alguno de mis compañeros para robarles algunas fotos, completo el artículo.
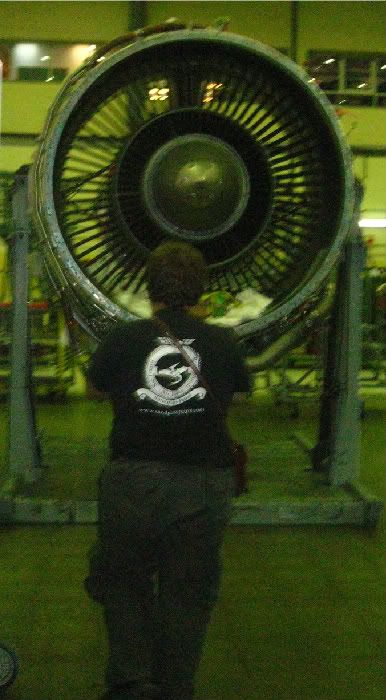
Aerotrastornados.com también ha publicado ya su resumen y su flickr, la entrada de LandingShort o las fotos de Wicho, Nacho y Angel
Descubre más desde Sandglass Patrol
Suscríbete y recibe las últimas entradas en tu correo electrónico.